Packing machines for valve bags
Setting new standards in the food industry
The efficient filling of your powdered food products requires a special know-how. Precision in this context not only refers to the accurate dosing of your high-quality products but also to the ability to transform them into real eye-catchers while maintaining strict hygiene standards!
Pro Tip: For easy handling and particularly appealing bag formats, opt for our valve bag technology. This way, as a food producer, you can impress with excellent filling results from planning and dosing to product packaging.
Users confirm
This is why our valve bag solutions stand out
- Clean product processing thanks to our inflatable sleeve on the filling spout
- Profit maximization through weight-accurate product processing
- Maximizing benefits through improved product and moisture protection
- Lower costs thanks to a clean packaging environment and low cleaning effort
- Higher advertising impact through optimally filled bags
- Effortless further processing of the bags
The customized filling system, which takes into account both the specific requirements of your food product and the properties of your valve bag, is crucial for the optimal processing of valve bags.
Rely on our valve bag filling systems - pneumatic and impeller packers - for food filling, which are your guarantee for efficiency, precision and reliability. They can be easily integrated into existing production lines and can be adapted to various bag sizes and materials.
Our pneumatic packer
The all-rounder for valve bags
The pneumatic packer ensures equal product discharge from the filling chamber through the conveying air quantity, which can be adjusted depending on the product. During the filling process, the special BEHN + BATES filling nozzle extracts the air from the bag.
Our impeller packer
The fastest filling technology for powder
Our impeller packer stands for fast and low-dust filling, also of fine powdered and easily flowing products. Your product is decisive for the choice of a vertical or horizontal impeller wheel as well as the design of the impeller wheel diameter.
Your advantages at a glance
- Weight-accurate filling due to coarse and fine dosing
- Increased product protection during filling by metal detector, integrated in the filling channel, with test device for different types of metal
- Reduced maintenance due to use of low-wear components
- Dust-tight sealing of the bag to be filled by the BEHN + BATES filling spout with inflatable sleeve
- Low cleaning effort due to minimum residual product quantities
Our ultrasonic sealing station
An integral part of our valve bag filling machines
Your products only meet the quality required on the market if they arrive at your customers perfectly protected from external influences. To ensure that this is the case, we equip most of all our filling machines that leave our production with our ultrasonic sealing station. It seals all PE-coated valves cleanly and tightly directly at the filling spout.
The history of the valve bag technology begins with the stationary packaging machine. The pioneer, our stationary packer ELEMENTRA®, scores highly among our customers worldwide with its intelligence, profitability and cleanliness. And this has been the case for decades.
For filling, the bag is applied onto the filling spout manually or automatically. The product is filled using the product-specific filling technology (air or impeller) designed to suit your product. Depending on the machine type, the filled bag is either removed manually from the spout or discharged fully automatically.
Your advantages at a glance
- Suitable for low up to the medium output segment, expandable up to 4 filling spouts
- High-quality standard equipment, customizable to your preferences
- Comprehensive digital setup for digital services such as monitoring, diagnostics and remote work, either available or expandable later
- Enhanced product protection through an integrated optional metal detector in the filling spout
- Reduced maintenance through the use of low-wear components
- Dust-tight sealing of the filled bag through the BEHN + BATES filling nozzle with an inflatable sleeve
Reduced machine noise, a clean working environment: the entire process of bag application, filling and sealing takes place in a dust-tight encapsulated cabin. Our Plug'n Pack concept also enables a quick machine setup at your production location.
The INTEGRA FD® is available with 1 to 4 filling nozzles, expandable for your flexible production planning. Depending on the product, we equip it with suitable filling technology—either air or impeller.
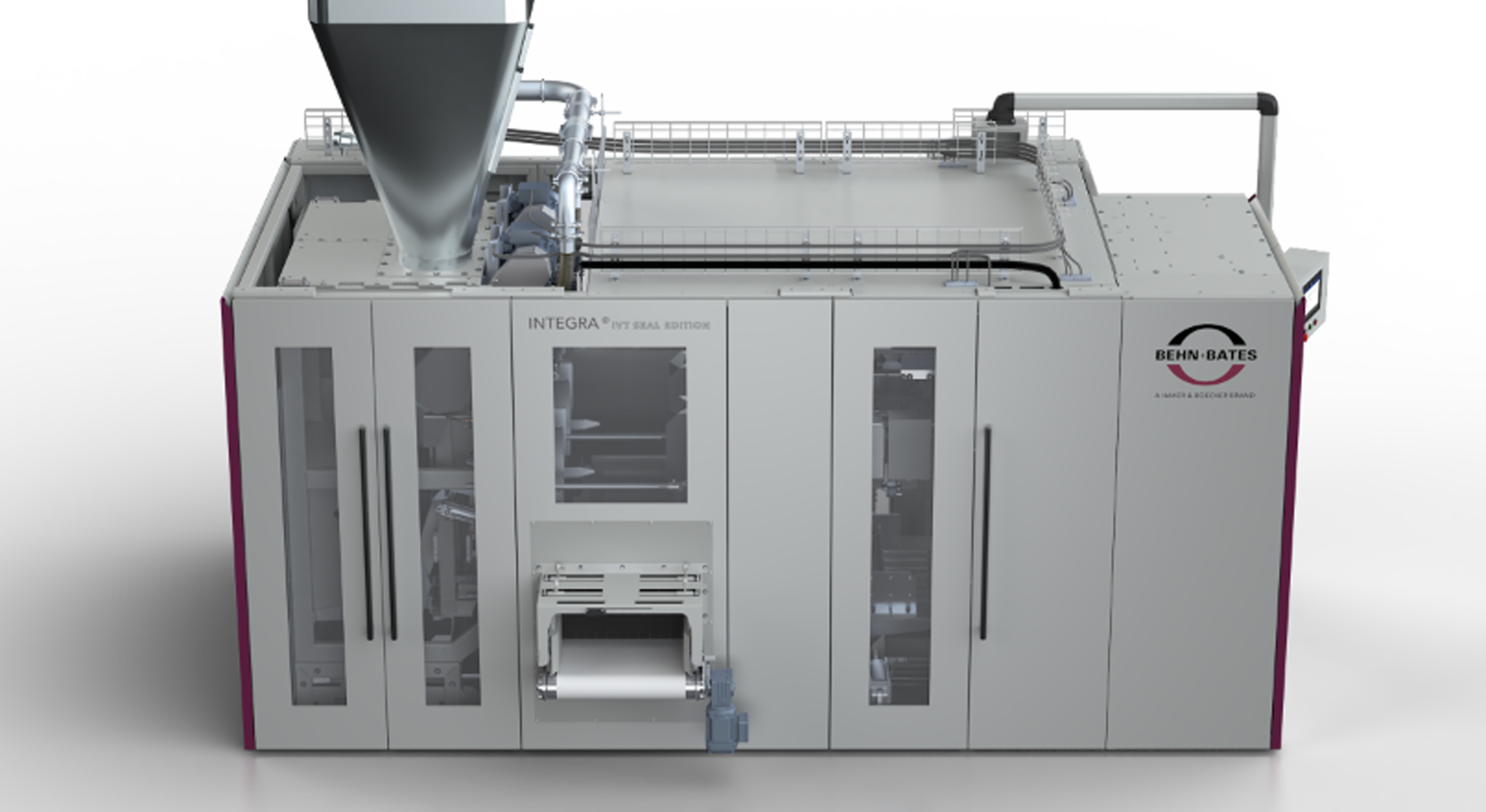
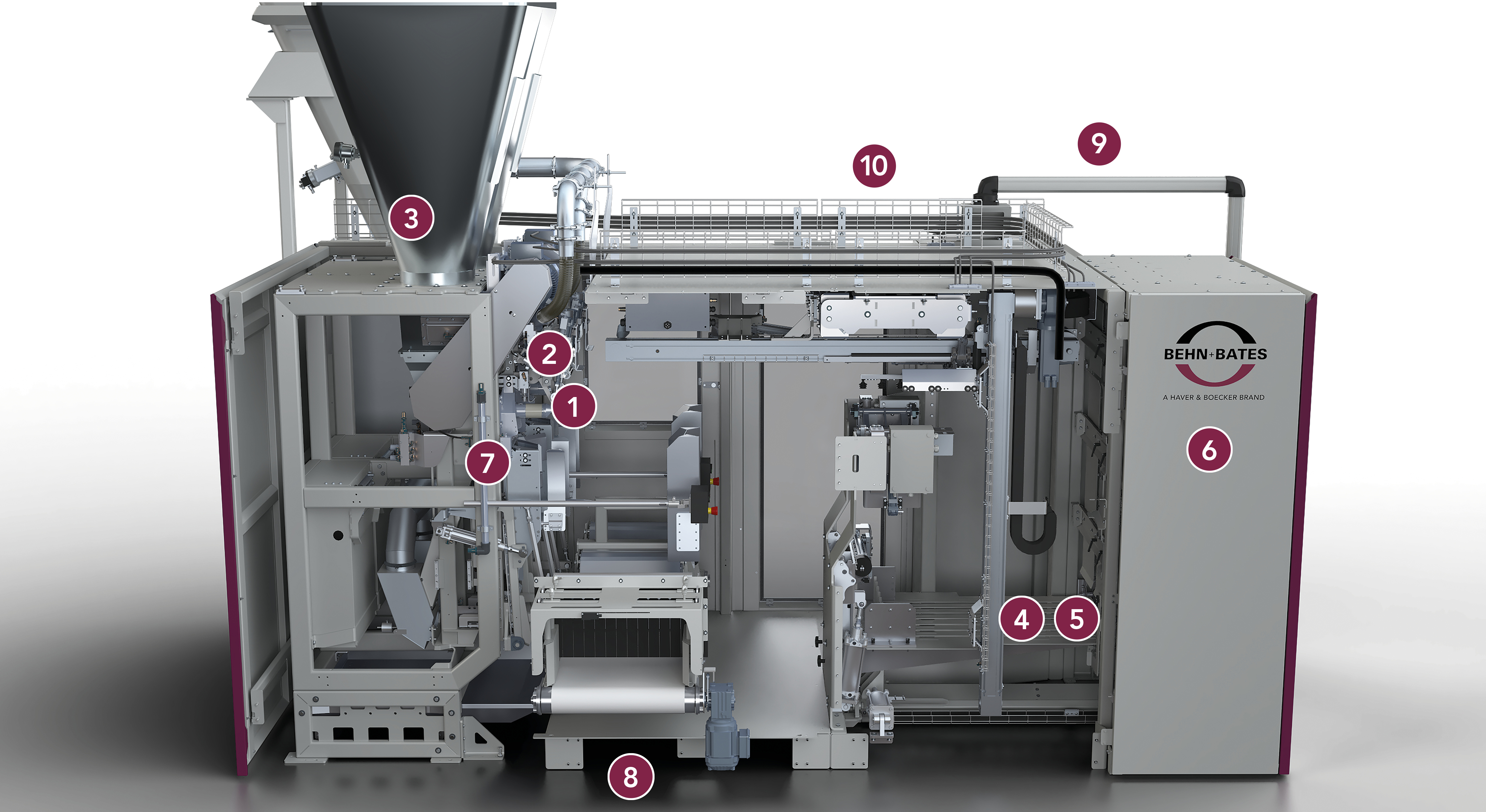
Behn+Bates INTEGRA® - Plug 'n Pack
Steamed machine noise, clean working environment: thanks to our Plug 'n Pack concept, the entire plugging, filling and closing process of the valve bags takes place in a dustproof encapsulated cabin.
New standards
1. reduced overall energy consumption
2. higher performance
3. cleaning-optimized design
4. improved accessibility
5. flexibility in use
6. Smart and digital solutions
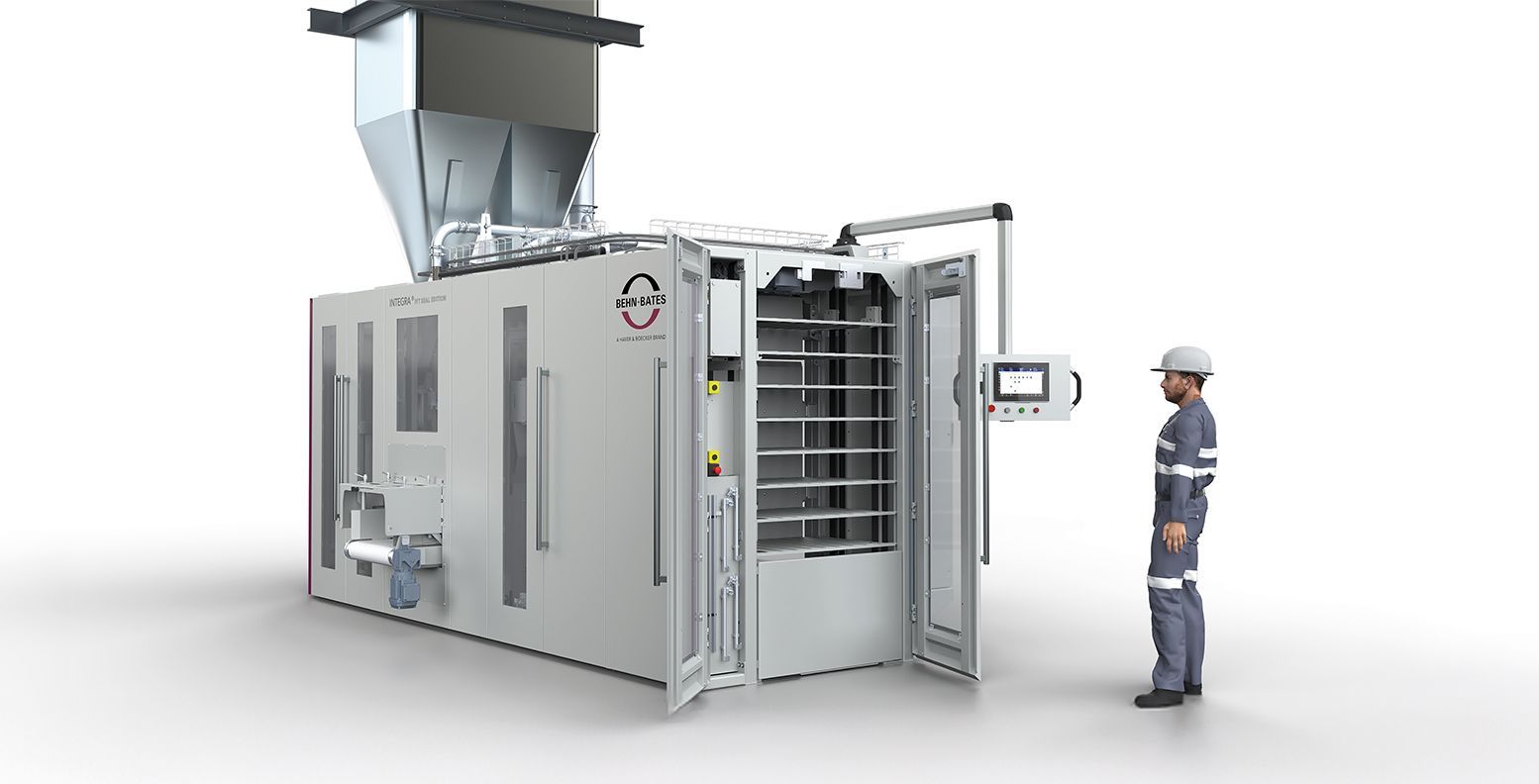
New modern HMI
-
15,6‘‘ Full HD
-
Remote access via PC, smartphone, tablet and browser
-
ATEX certificated (optional)
-
PDF and website display possible
-
Customizable login
-
System messages with comment function
-
New recipe management
-
Logbook function
-
Switch of HMIs within a line
-
Multi-touch - swipe and zoom function
Energy efficiency
-
Reduced total energy consumption by up to 2.5%
-
Energy-saving and switch-off mode for process units
-
Utilization of braking energy
-
Optimized dust extraction volume
Maximum availability
-
Wear-free servo drives
-
Use of OEM identical parts and systems
-
Assured spare parts supply
Increased performance
-
Up to 10% higher performance
-
Faster cycle due to diagonal movement of the attachment arm
-
AI-supported camera technology for optimized attachment rate (optional)
User-friendliness
-
15.6-inch touch control panel
-
Modern, web-based HMI
-
Standardized operating concept
-
Tidy interior design and large window
-
Diagnostic lighting (optional)
-
RFID sticks
-
MEC IV weighing control device
Improved accessibility
-
Swivel-mounted control cabinets (optional)
-
Protected cable routes on the roof
-
Simple settings thanks to pneumatic shaft
-
Transformer function (optional)
-
Large openings and doors
Easy maintenance
-
Centrally arranged pneumatics, also accessible during operation
-
Easy-to-open, accessible cladding elements
-
Cleaning-optimized positions in maintenance mode
Flexibility in use
-
For every HAVER & BOECKER filling system with 1-4 filling spouts
-
Larger range of bag lengths and widths
-
New clip-on claw for different valve sizes
-
Three magazine variants for empty bags
-
Standardized motor system
-
Suitable for hygiene and pharmaceutical applications
-
Variable arrangement of the spouts
-
Separate installation of control panel (optional)
Hygiene and cleaning
-
Up to 50% time saving during cleaning
-
Cleaning-optimized design of the bundle magazine (optional)
-
AI-supported camera technology for fewer bag bursts (optional)
-
Systems for various hygiene applications
-
Hygienic design and installation
Smart and digital solutions
-
digital QUAT2RO® solutions (optional)
-
AI-supported process performance
-
modern, web-based HMI
Highest bagging capacities of up to 2,400 bags/h can be achieved with our ROTO-PACKER® for valve bags. The filling spouts on the ROTO-PACKER® are mounted on a rotating frame. This results in a reduced space requirement. The bags can be placed on the filling spouts both manually or automatically by our RADIMAT® bag applicator. Before discharge, bag sealing is possible directly at the filling spout, using our ultrasonic sealing station.
Our ROTO-PACKER® works with the correct filling system for your product: air or impeller. You decide how many filling spouts your ROTO-PACKER® will have: what counts is performance or also your desire for expandability at a later date.
Your advantages at a glance
- Cost efficiency due to a central product supply and a central full-bag transport system
- Improved economic efficiency due to a higher performance in a small space
- Clean product handling thanks to the product-specific filling system and ultrasonic sealing directly at the filling spout
- Reduced maintenance efforts due to continuous gentle operation of downstream units
- Simple automation with the RADIMAT® valve bag applicator
- Successive increase in production due to the extendable machine design - without changes to the periphery
- Higher maintenance efficiency due to individual filling spouts that can be switched off